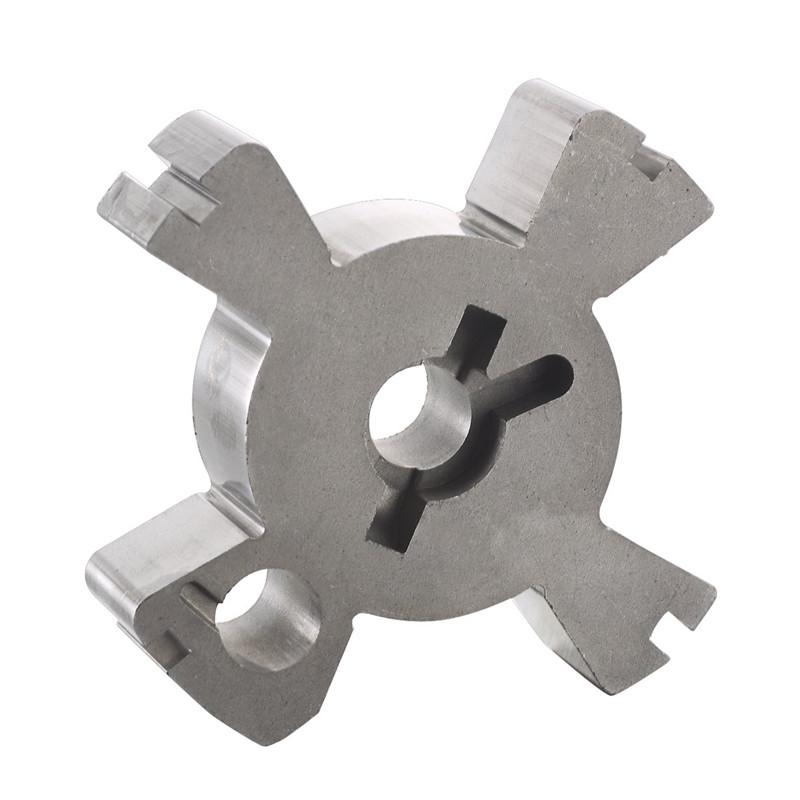
Powder sintered auto parts are made by melting metal pa […]
Powder sintered auto parts are made by melting metal particles and then heating them up in a furnace. These auto parts are commonly used in the steering mechanism, exhaust system, transmission, and engine. Metal powder is commonly made of iron and steel. The powdered metal is then mixed with alloys and additives and solid lubricant powders, such as amide wax, to form a composite part. These components are used in many different applications, such as in engines, transmissions, and other vehicle components.
After compiling the raw materials, the powder is heated in a furnace, and the resulting part has a very high degree of symmetry. Then, it is compacted to make it into a solid. The finished part appears to be solid, but is actually comprised of thousands of tiny capillaries with a 25 percent porosity. During the process of manufacturing powdered metal auto parts, manufacturers consider several factors, such as the application, size, shape, and complexity of the part. They also take into account the environment, frequency of use, and volume of the product.
Compared to traditional manufacturing processes, PM parts have favorable cost, precision, and physical properties. They are easily automated and have complex shapes. Because they are a composite, PM components are easier to manufacture than their traditional counterparts. Further, the process can be fully automated, meaning that PM auto parts can be produced in very short run. The advantages of PM include lower production costs, greater consistency and reliability, and less waste. There are many advantages to this type of manufacturing.
The manufacturing process used to create these parts is complex. A lot of raw materials are compacted. After sintering, they are bonded together while maintaining their shape. The finished product, called a green part, appears solid, but is actually a combination of tiny capillaries and has a 25 percent porosity. Most powdered metal part manufacturers take the following into consideration: the material's composition, application, and temperature, and the volume of the product.
Powder metal is soft and pliable. It can be shaped into different shapes, and is a great material for car parts. Because it's soft, it is a popular choice for magnetic parts. The sintering process also improves its magnetism. These parts are used in a wide range of industries. These auto parts are made by sintering, powder forging, and powder spraying.
PM components are often made of steel, aluminum, and other metals. This material has the advantage of being able to be molded into complex shapes. Furthermore, the material is soft and malleable. In fact, PM parts are often the most cost-effective option. Further, these auto parts are highly customizable and will last for years. Consequently, they can be used in any type of vehicle. There are many benefits to using powder metal.