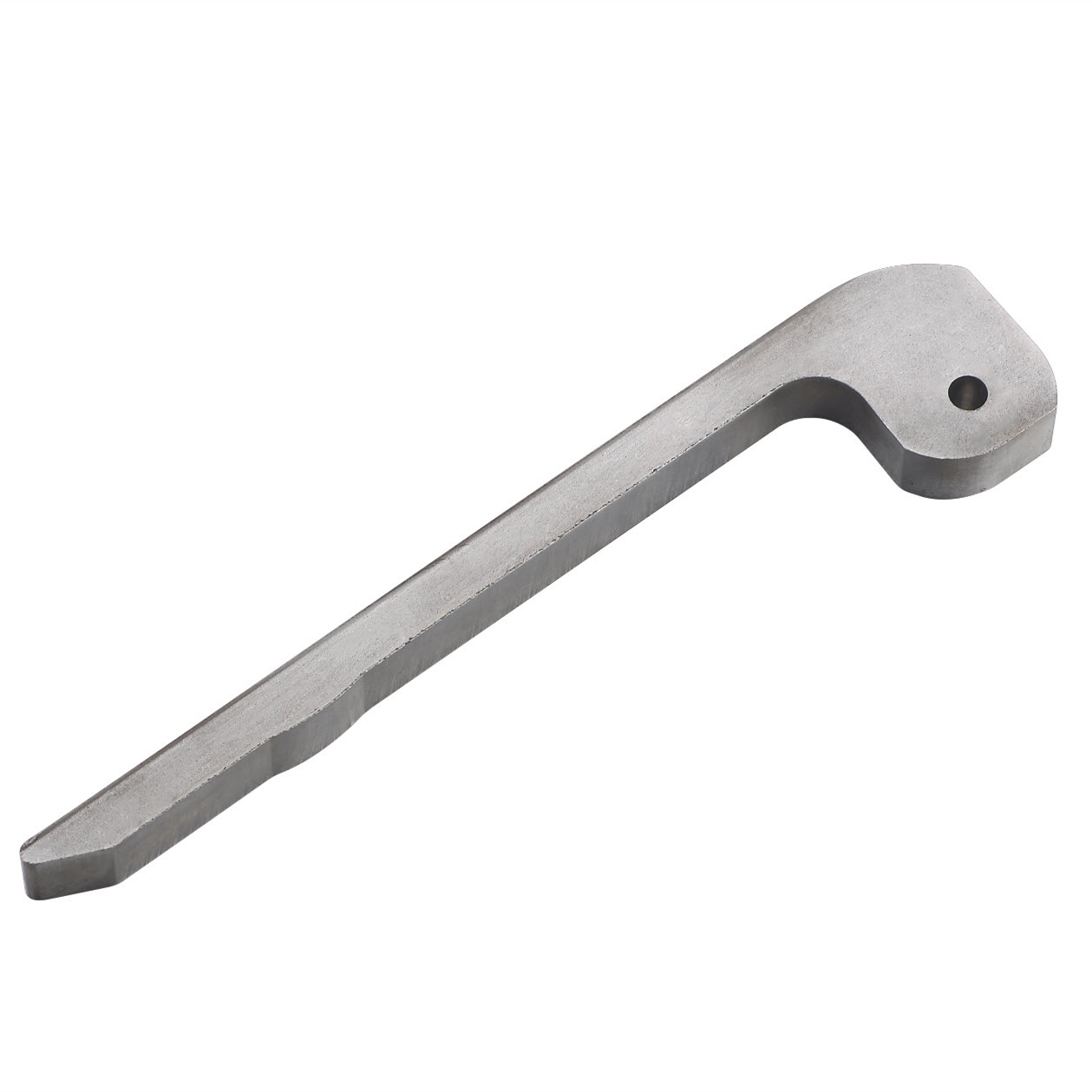
About 80% of all powder metallurgy parts used are for a […]
About 80% of all powder metallurgy parts used are for automotive applications alone. About 25% are used for transmissions and nearly as many are used for engines. These transmission applications usually include transmission panes, clutch hub assemblies, carrier bushing kits, and gear shifts. Common accessories that are used in these applications include clutch plates, clutches, piston rings, carrier bushings, pinion nut holders, pinion gears, and valve stem. In addition to these products, there are many more options available and some people specialize in only a certain type of machine application.
For example, there are a type of powder metallurgy parts called porosity parts and they are sometimes used for very specific purposes. Some of the most common applications of this type of material are in the automotive industry for casting or forming metal parts with high production tolerances. Other uses include forming sheet metal pieces and forming metal screws, bushings, bolts and nuts. The materials that are used for high production tolerance parts often have a higher ratio of porosity to hardness. Because of the high production of this type of material, there is a need to form it into intricate parts that can withstand high levels of heat.
In addition to forming powder metallurgy parts into intricate parts, there is also a need to make sure that these parts have good resistance to corrosion. In order to perform this, manufacturers must create casing and plug sets that will work properly in conjunction with each other and they must use special grease that allows the components to move with ease without any friction or abrasion. The final product that is created from the powder forms is often referred to as bearing caps and these are used to seal bearings and to form balls and rings that can be used for a variety of different applications in industries like automotive, marine and construction. These parts can also be used in military applications such as laser rangefinder controls, laser pointers, vehicle tires and military pistol magazines.
Other examples of powder metallurgy parts that can be used in industrial applications are pipe fittings and camshafts for automotive applications, valves for gas or oil-fueled engines, rotors and bearings for vehicles and turbines, rings for watches and necklaces for accessories. These types of components are also popular in hobbyist and professional markets because of the wide variety of finishes and models that are available. There are many custom finishes that can be created for a particular product depending on what is needed and the manufacturer's discretion. This means that there is a product for every need and for every situation.
The final products that are produced from powder metallurgy parts come from a process called heating. After all of the individual particles have been pressed together and into their appropriate shapes, they are heated until they reach a critical temperature. This process is necessary because it makes it possible to create metal particles that are stronger and more malleable than their raw counterparts. After the individual particles have reached the right temperature, they are then able to be manipulated by a pressing machine. Any products that are press pressed can have different finishing processes applied so that the finished product will have the ability to match the original design as closely as possible.
Powder metallurgy is a very unique type of pressing that has created a huge boom in the manufacturing industry. It allows manufacturers to press raw components into precise shapes, which are then put through a series of different processes until the final product is ready for sale. In addition to having a diverse use in the manufacturing industry, isostatic pressing is ideal for a number of hobbyist activities. Whether you want to press mechanical components, or make your own custom-designed parts, isostatic pressing is the perfect way to do it.